


-
-
LED Aluminum Light Pole M-TF-G Click: , Update:Aug 20, 2012
-
aluminum Pole Light M-LA-183S Click: , Update:Aug 20, 2012
-
aluminum light China M-LA-183 Click: , Update:Aug 20, 2012
-
Aluminum flag poles Click: , Update:Aug 20, 2012
-
Aluminum Lamp Pole M-TZ Click: , Update:Aug 20, 2012
-
Aluminum light poles M-TD Click: , Update:Aug 20, 2012
-
Aluminum light pole M-TJ Click: , Update:Aug 20, 2012
-
Aluminum Pole Flag Click: , Update:Aug 20, 2012
-
aluminum Pole Light M-LA-183D Click: , Update:Aug 20, 2012
-
Aluminum light pole M-TS Click: , Update:Aug 20, 2012
-
fence NT-SF-MD6 Click: , Update:May 26, 2012
-
Flag post Click: , Update:May 16, 2012
-
Aluminium banners flag poles Click: , Update:May 15, 2012
-
Street Light Lamps Click: , Update:May 14, 2012
-
aluminum light China Click: , Update:May 14, 2012
-
banner flag pole Click: , Update:May 15, 2012
-

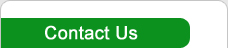


|
Detailed Product Description
MRC is a professional manufacturer of aluminum light poles,aluminum lamp poles,light poles,lamp poles,lighting pole,pole light light post,outdoor light post,outdoor lightin,led post light,street poleMRC supplies excellent quality, competitive price and best service.
Specifications
The aluminum lighting pole takes advantage of its permanence of non-rust, multiples way of surface treatment, less material cost, succinctly smooth lines and other characteriestics to make up 0 shortcomings from traditional lighting pole; It is easy to rust, the design isn't diverse, the surface is quite rough, the mold cost is high, ther environment-protective is bad and so on.
Apply to garden, street, residence, square, school, restaurant and so on.
In China, NANTIAN is the first manufacturer bringing in modern spinning technology to produce aluminum alloy poles. Our aluminum lighting pole and aluminum flagpole are used body formation craft, solid, safe, durable, environmental. Surface is treated with anodic oxidation, becomes clear, colorful and delicate surface. We also customize to anyone who has large demand.
M-LA-183D | ||||
Item | Height (m) | Top diameter (mm) | Bottom diameter (mm) |
Base plate (mm) Length/Holes Pitch/THK |
M-LA-183/8.0 | 8.0 | 85*4.1 | 183*4.1 | 300/260/18 |
M-LA-183/8.5 | 8.5 | |||
M-LA-183/9.0 | 9.0 | |||
M-LA-183/10 | 10 | |||
M-LA-183/11 | 11 | 85*4.1 | 183*4.1 | 300/260/18 |
M-LA-183/12 | 12 | |||
OD range: 60mm~230mm
Material: Aluminium 6063
Finish:
1. Anodised or keep primitive colours (polishing or brush)
2. Powder coating
3. Spray-paint
Various kinds of styles for choice, contact us for more info.
1.Corrosion resistant
2.Maintenance free
3.Lighter weight for easy and cost efficient installation
4.various finishing
5.longer life than steel and Fiberglass
6.100% recyclable, aluminium melting temperature is low to save energy and reduce emission
7.direct buried applications
8.less deflection than fiberglass poles.
correlation table:
Product | Advantage | Shortcoming |
Steel poles | strength |
l Visible rust and corrosion l Weights three times as aluminium and high freight cost l Limited recycle value l Should not be direct buried l Limited finishing |
Fiberglass poles |
Light weight Can be direct buried |
l Short life l No recycle value and difficult and expensive to dispose l Ultraviolet damage is common l Expensive maintenance costs l Can be damaged by mowing& trimming |
Concrete poles |
Can be direct buried Strength Never needs painting |
l Heavy and expensive shipping costs l No recycle value l Difficult to install and require expensive installation equipment l More dangerous than other material |
Producing Process
1,material
The materials used for spinning are straight round 6061 or 6063 aluminum pipe. They’re excellent extruded profiles for architecture and widely used as aluminum windows and doors construction, wall frame and so on. They have a high wind resistance performance , fabricated performance, corrosion resistance and decorative properties.
2, forming polesRaw materials, through large non-mould CNC spinning equipment, are formed conic or abnormity poles in the process of high-speed rotating. In the following, the formed poles will be polished to remove oils, glitches, and indentation on surface. All the poles do not have longitudinal weld.
3, welding of base plate
In order to ensure the strength of the base, all base plates are 6061 or 6063 aluminum alloy sheet pressed by special mould or cast aluminum A356. Automatic welding is used to weld the base plates of the poles. In this high-quality welding process, strength and aesthetics are guaranteed.
4, access door
Each light pole has an access door for the installation of the electrical junction box. We use advanced cutting machine to cut the door, so the door is part of pole and is tightly matched, and the crack gap is even, which guarantee the door waterproof. Generally access door is 500mm up from the ground in the poles (also may based on the shape of poles). At the back of door, that is inside the pole, there’s a aluminum rail welded for fixing the junction box. Lock is specially made with stainless steel anti-theft screws, and only professional tools provided can open, thereby this enhances the product's security performance.
5, grounding systemuse a "L"-shaped folded aluminum workpiece, one side is welded to the wall of the pole, on the other side, drill a M8 hole in the center for the grounding wire.6, connection of subsection polesTwo-sections poles use special linked clamp to connect. Clamp is made up of four U-shaped pieces and screws, the screws are M8 * 45.7, temper treatmentTo ensure the strength aluminum alloy, all of our aluminum poles will be subject to quench aging treatment to T6 grade to comply with international strength standard for aluminum pole.
8, anticorrosive protection of the root section
The lower part of the poles should be protected from salt alkaloid ingredient corrosion in the soil and mechanical damage. The protection coating and the way of production are environmentally friendly. MRC cover the pole base and the lower part of poles up to 350mm in height with epoxy resins. All directly-buried poles base cover epoxy resin and the thickness between 0.7mm-1.0mm.
9, surface treatment
(one), anodic oxidation
MRC offer anodized finish as standard because it provides the best quality product . Brushed poles cannot offer the same lever of protection and easily blacken in polluted aggressive environments such as coastal corrosion areas, traffic intersections and salted road are susceptible to corrosion. Anodizing is used to protect the aluminum surface of poles, extension arms and ornamental motifs from corrosion.
Anodizing is an electrochemical method which creates an oxide layer on the surface of the metal. Anodized coatings are supplied in several thickness of coating appropriate to the installation location and local conditions. The standard anodized coating is 12microns and this ensure safe use in moderate to harsh conditions.
anodic oxidation process of general profile as follows: degreasing—washing--washing-- caustic washing --washing ---washing --- bright---washing ---pure water washing-- anodic oxidation---washing---Washing-- coloring (electrolytic / chemical )---- washed washed ----sealing
(A) degreasing
No matter how you process the aluminum products, the surface will exist in varying degrees, dirt and defects, such as dust, metal oxides (oxide film formed under natural or high temperature ), residual oil, asphalt signs, artificial Handling fingerprints (the main component is fatty acids and nitrogen-containing compounds), welding flux, as well as corrosive salts, metal burrs, scratches and other minor draw. Therefore, prior to oxidation treatment, it is necessary to use chemical or physical methods to clean the surface of the products in order to expose metal matrix to do oxidation coloring and get the artificial membranes, which is combined with the solid matrix. Its color and thickness will meet the requirements and it has the best corrosion resistance, wearable , weatherproof performance
(B) Alkali etching (caustic washing)
Alkali etching is the process that wash the surface of aluminum products in the sodium hydroxide solution within or without other substances, also known as alkali corrosion or caustic washing. Its role is to make up degreasing and do further cleaning, to remove natural oxide film and minor abrasions on surface. So that products expose clean metal matrix which is conducive to the generation of anodic film and has a high-quality film. In addition, by changing the composition of solution, temperature, processing time and other operating conditions, we’ll have smooth ,satin-matt, gloss or other kinds of corrosion washing surface.
(C) bright (neutralization)
the gray or black hanging ash which attach on surface of aluminium products after Alkali etching will not be dissolved in the cold or hot water, but can be dissolve in acidic solution, therefore, after Alkali etching, products should wash in acid solution in order to remove the hanging ash as well as residue lye and expose bright basic metal surface, this process is called neutralization, or bright processing.
(D) anodizedaluminum or aluminum alloy products as the anode is placed in electrolyte solution (sulfuric acid solution commonly), through electrolysis, to make aluminum oxide film formed on the surface, this process is known as anodized.
(E) colouring
1, chemical coloring Chemical coloring process is simple, easy to control, having a wide color range and the color is bright.(1) monochrome staining: immerse aluminum products which is finish anodic oxidation and washing into the dye liquor that is in stated temperature.
(2) multi-color staining: two or more colours are required on aluminiun products , such as landscapes, flowers and birds, text, mainly use printing process to complete.
2, electrolytic coloring Electrolytic coloring process is sun-proof and hard to fade, it is the most widely used method of coloring.Through changing the dyeing time, we may gain yellow, champagne, bronze colour , brown ,black and so on.
(Vi) sealing
In order to improve the quality of aluminum and dyeing, the micro-porous of the oxidized film should be closed after colouring. After sealing treatment the surface becomes even and non-porous and form a dense oxide film. Dye depositing in the oxide membrane is indelible. And the oxide film has no adsorption, which will avoid being contaminated by absorption of harmful substances and early erosion, thus it improves anti-pollution and anti-corrosion of anodic oxide film. Commonly hydrated sealing way, inorganic salt solution sealing way, transparent organic coating sealing way after dyeing are available.
Features of anodized pole:Anodized layer is part of metal surface, which will not peel and flake, and the color won’t fade;
Long life: through anodic oxidation treatment, product forms a 12μm sealing film in order to ensure the poles to resist corrosion in nature and no significant discoloration in 25 years. (B), fluorocarbon coating A new coating material, it has excellent anti-fade, anti-frost, anti-air polluted (acid rain, etc.) corrosion, anti-UV ability, and strong anti-crack and the ability to withstand harsh weather conditions that the general coating can’t reach.
(C), powder coatingLight pole surface can be colored polyester powder coating, bright color, anti-ultraviolet radiation, non-fading.
Note: Because rod body, boards, wire and other material differences, anodizing would produce a certain color,
NOTICE: Anodizing inherently results in color variations on aluminum as the material difference between the poles, the base and the welding material, it is inevitable. If you want to ensure the color consistency on surface of poles, powder coating or fluorocarbon coating is recommended.
